Performance parts, a crucial element in automotive enhancement, offer a spectrum of upgrades that significantly boost vehicle performance. From engine modifications to suspension tweaks, these parts can dramatically alter a car’s handling, acceleration, and overall driving experience.
This comprehensive guide delves into the intricacies of performance parts, examining their various types, materials, installation, and safety considerations. We’ll explore the benefits and drawbacks, market trends, and the essential factors to consider when choosing and using these components. Whether you’re a seasoned enthusiast or a curious novice, this resource provides a clear and insightful understanding of performance parts.
Defining Performance Parts
Performance parts in the automotive industry are components designed to enhance a vehicle’s performance beyond its standard specifications. These parts are meticulously engineered to optimize specific aspects of the vehicle’s operation, improving acceleration, handling, braking, and overall driving experience. They are often tailored for specific driving styles and needs, from spirited road driving to track performance.These modifications can be categorized based on their intended function, impacting various systems of the vehicle.
This allows for a focused approach to enhancing specific performance attributes. For example, engine components are crucial for power output, while suspension parts affect handling and ride comfort. The diverse range of performance parts available caters to a wide spectrum of automotive enthusiasts and drivers.
Performance Part Categorization by Function, Performance parts
Performance parts are categorized based on the specific vehicle system they enhance. This approach allows for a tailored enhancement to specific performance aspects. For instance, engine parts focus on power output, while transmission parts optimize shifting performance.
- Engine Performance Parts: These components are designed to increase horsepower, torque, and responsiveness of the engine. Examples include upgraded intake systems, exhaust systems, and performance air filters. High-performance engine components, such as turbochargers and superchargers, can dramatically increase the engine’s power output. This often requires matching modifications to other components for optimal performance.
- Transmission Performance Parts: These parts are crucial for smooth and quick gear changes. Performance-tuned clutches, upgraded transmissions, and shift kits are examples, enhancing the responsiveness of the vehicle during acceleration and shifting.
- Suspension Performance Parts: These parts directly affect handling, ride quality, and cornering performance. Examples include performance springs, shocks, and sway bars. These modifications often improve a vehicle’s stability and agility during driving.
- Braking Performance Parts: Performance brake systems improve stopping power and response. High-performance brake pads, rotors, and calipers are examples of components that enhance braking efficiency and responsiveness. The ability to stop quickly is critical for vehicle safety.
- Exhaust Systems: These components improve engine performance and provide a distinctive sound. Performance exhaust systems are often designed to reduce backpressure and increase exhaust flow, which results in enhanced power and acceleration. However, they can also create a louder exhaust sound.
Distinguishing Performance Parts from Standard Parts
Performance parts are fundamentally different from standard parts in several key aspects. These distinctions stem from the rigorous engineering process focused on enhanced performance.
- Materials and Construction: Performance parts often utilize advanced materials and construction techniques to achieve enhanced strength, durability, and performance. This is often achieved through lighter materials and stronger alloys.
- Design and Functionality: Performance parts are specifically designed to optimize specific aspects of vehicle operation. They are often engineered to enhance power, handling, or other performance metrics.
- Performance Metrics: Performance parts are rigorously tested and evaluated to ensure they meet or exceed specific performance criteria. This includes acceleration tests, braking tests, and handling evaluations.
Comparison of Standard and Performance Parts
The following table illustrates the key differences between standard and performance parts across various vehicle systems.
Vehicle System | Standard Part | Performance Part | Key Differences |
---|---|---|---|
Engine | Stock engine components | Upgraded pistons, forged crankshafts, performance camshafts | Increased horsepower, torque, and responsiveness |
Transmission | Standard transmission | Performance clutch, short-throw shifter, performance transmission | Faster shifting, smoother gear changes |
Brakes | Standard brake pads and rotors | High-performance brake pads, performance rotors, upgraded calipers | Enhanced stopping power, shorter stopping distances |
Suspension | Standard springs and shocks | Performance springs, upgraded shocks, stiffer sway bars | Improved handling, reduced body roll |
Performance Part Materials and Manufacturing: Performance Parts
Performance parts, designed for enhanced functionality and durability, necessitate careful consideration of materials and manufacturing processes. These components often operate under demanding conditions, requiring exceptional strength, lightweight properties, and resistance to wear and tear. The selection of materials and the manufacturing techniques employed directly influence the part’s overall performance and lifespan.
Material Selection for Performance Parts
The choice of materials is crucial for performance parts. Different materials exhibit unique properties, such as strength, stiffness, and heat resistance. High-performance applications frequently utilize advanced alloys, composites, and specialized polymers. For instance, titanium alloys are favoured for their high strength-to-weight ratio in aerospace applications, while carbon fiber composites are employed for their lightweight nature and high stiffness in sports equipment.
Manufacturing Processes for High-Performance Parts
Advanced manufacturing techniques are employed to achieve the desired properties and precision in performance parts. These methods often involve sophisticated processes like precision machining, additive manufacturing (3D printing), and forging. Precision machining, with its ability to create complex geometries and tight tolerances, is essential for parts requiring intricate shapes and high accuracy. Additive manufacturing allows for the creation of intricate shapes with complex internal structures, often leading to lightweight designs.
Durability and Lifespan of Performance Parts
Performance parts, owing to their enhanced design and material selection, typically exhibit superior durability and lifespan compared to standard parts. Factors such as material strength, manufacturing precision, and environmental conditions all play a significant role. For example, a high-performance engine piston, constructed from a heat-resistant alloy and subjected to precision machining, will generally demonstrate a longer lifespan and better performance than a standard piston under similar operating conditions.
Moreover, proper maintenance and operational conditions are vital in maintaining the longevity of any performance part.
Engineering Principles in Performance Part Design
The design of performance parts is grounded in fundamental engineering principles. These principles ensure optimal performance under the intended operating conditions. A critical consideration is stress analysis, which determines the material’s ability to withstand applied forces without failure. Furthermore, fatigue analysis evaluates the part’s resistance to repeated loading, crucial for components subjected to cyclic stress. By integrating these principles, engineers can create high-performance parts that meet stringent performance criteria and ensure extended service life.
Performance Part Benefits and Drawbacks
Performance parts are often sought after by vehicle owners seeking enhanced performance and handling characteristics. These modifications can significantly impact a vehicle’s capabilities, but it’s crucial to understand both the advantages and potential drawbacks before undertaking any upgrades. Choosing the right performance parts for a specific vehicle requires careful consideration of several factors, as modifications can have unforeseen effects.Understanding the interplay between these enhancements and the original vehicle design is essential for maximizing the benefits and mitigating any negative consequences.
This evaluation considers the impact on vehicle handling and performance, along with the specific factors influencing part selection.
Advantages of Using Performance Parts
Performance parts can deliver notable improvements in various aspects of vehicle operation. Enhanced power delivery and acceleration are common benefits, achieved through modifications like upgraded engine components. Improved handling and responsiveness are also notable outcomes, often resulting from modifications to suspension components and steering systems. These improvements can translate into a more engaging driving experience.
Performance parts are all about boosting a car’s capabilities, but they’re ultimately just a subset of the wider world of auto parts. From engines to exhaust systems, everything contributes to the overall driving experience, and choosing the right performance parts can make a real difference. Ultimately, the goal is to optimize the car for better performance.
Potential Drawbacks of Using Performance Parts
While performance parts offer potential advantages, it’s essential to acknowledge the potential drawbacks. Increased fuel consumption is a frequent consequence of modifications that enhance power output. This can result in higher operating costs. Reduced reliability is another potential concern, as aftermarket parts may not always meet the same stringent quality standards as OEM components. Mismatched components can also negatively impact the vehicle’s overall performance, necessitating further modifications to achieve the desired effect.
Furthermore, installing incompatible performance parts might void the vehicle’s warranty.
Impact on Vehicle Handling and Performance
Performance parts can significantly influence vehicle handling and performance. Engine upgrades, for instance, can lead to increased horsepower and torque, resulting in quicker acceleration and higher top speeds. Suspension modifications can enhance responsiveness and handling by adjusting ride height, dampening characteristics, and tire contact patch. However, the interaction between different performance parts can be complex and potentially require further adjustments or upgrades to ensure optimal performance.
For example, installing a high-performance exhaust system without appropriately tuned engine management software might not deliver the expected improvements.
Factors to Consider When Choosing Performance Parts
Selecting appropriate performance parts for a vehicle requires a thorough evaluation of various factors. Matching the part to the vehicle’s specific model and year is crucial. Consider the vehicle’s existing mechanical condition; poorly maintained components might not function optimally with added performance parts. Researching the compatibility of the performance part with the vehicle’s existing components and systems is paramount to avoid unforeseen complications.
Compatibility issues can arise with exhaust systems, engine management systems, or suspension components. Ultimately, the decision should weigh the desired performance gains against potential costs and risks.
Performance parts are a great way to boost your ride, but proper installation and maintenance are key. Knowing how to handle potential issues is crucial, and a good understanding of auto repair principles can save you headaches down the line. Ultimately, it’s important to remember that even the best performance parts need careful attention for optimal results.
Performance Part Installation and Maintenance
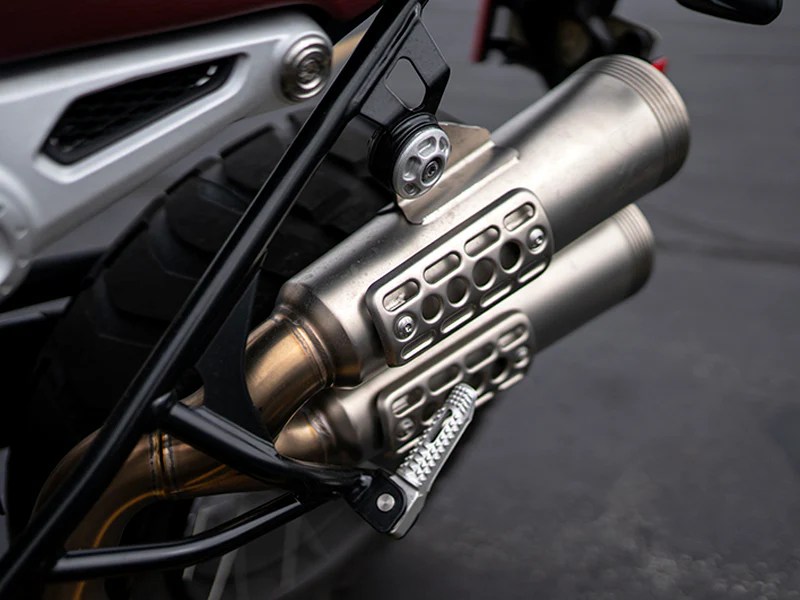
Proper installation and maintenance are crucial for maximizing the performance and lifespan of performance parts. Neglecting these aspects can lead to reduced efficiency, potential damage to the vehicle, and voiding warranties. Careful attention to detail throughout the installation process is essential.
Correct Installation Procedures
Careful adherence to manufacturer guidelines is paramount for a successful installation. Following the specific instructions provided by the part manufacturer is essential to avoid damage and ensure optimal performance. This often includes precise torque specifications for fasteners, specific clearances for components, and necessary adjustments for proper function. Documentation should be reviewed thoroughly before starting any installation process.
Maintenance Requirements
Regular maintenance is key to preserving the performance and longevity of performance parts. This often involves inspecting components for wear and tear, checking for proper lubrication, and verifying the integrity of seals. The frequency of maintenance can vary depending on the specific part and the operating conditions. Adhering to recommended maintenance schedules is critical.
Importance of Professional Installation
Professional installation significantly reduces the risk of complications and potential issues. Certified technicians possess the expertise, tools, and knowledge to install performance parts correctly, ensuring optimal performance and safety. Improper installation can lead to unforeseen problems, affecting vehicle operation and safety. Professional installers are often familiar with the nuances of different systems, including those involving complex components or specialized tools.
Potential Issues with Incorrect Installation
Issue | Description | Potential Consequences |
---|---|---|
Improper Torque | Applying insufficient or excessive torque to fasteners. | Loose connections leading to vibrations, premature failure of components, or potential damage to the vehicle. Conversely, over-tightening can damage threads or components. |
Incorrect Clearance | Installing components with inadequate or excessive spacing. | Interference with other components, leading to binding or malfunction. Insufficient clearance can also cause excessive wear. |
Inadequate Lubrication | Insufficient lubrication of moving parts. | Increased friction, accelerated wear and tear of components, and potential failure. Dry friction can lead to significant overheating. |
Improper Alignment | Components not aligned correctly. | Reduced efficiency, increased vibrations, and potential damage to the system. |
Failure to follow manufacturer’s instructions | Skipping steps or not adhering to the specific installation guidelines. | Incorrect operation, reduced performance, and damage to components. Failure to follow proper installation can lead to significant problems that might be hard to detect initially. |
Performance Part Selection and Compatibility
Selecting the correct performance parts is crucial for optimizing vehicle performance and ensuring compatibility with the existing system. Improper selection can lead to reduced performance, potential damage to components, and voiding of warranties. Careful consideration of vehicle-specific needs and part specifications is paramount.
Criteria for Selecting Performance Parts
Choosing the right performance parts involves evaluating several key criteria. Engineered specifications, such as horsepower output, torque, and RPM ranges, are vital for matching the performance part to the vehicle’s engine characteristics. Compatibility with the existing vehicle’s drivetrain, including transmission, axles, and differentials, is essential to prevent mechanical issues. Consider the specific application, including track use or daily driving, and the desired performance gains.
Furthermore, the part’s material composition and construction should be assessed to ensure durability and longevity. Finally, consider the budget and the part’s expected lifespan to make an informed decision.
Determining Performance Part Compatibility
Ensuring compatibility is a critical step. Performance parts are often designed for specific vehicle models and years. Incorrect parts may not fit properly or function as intended, causing significant issues. Thorough research is necessary to identify the precise vehicle model and year for accurate part compatibility. Consult the manufacturer’s documentation or online resources for specific compatibility details.
Often, a part’s compatibility is explicitly stated by the manufacturer, allowing for a more precise assessment.
Importance of Checking Part Numbers and Specifications
Precise part numbers and specifications are critical for ensuring the correct part is selected. Incorrect parts may not meet the intended performance standards, causing issues with functionality or safety. Comparing part numbers from different manufacturers is crucial to determine whether the part is a direct replacement or a modified version, and whether it aligns with the intended application.
Detailed specifications, such as tolerances, materials, and dimensions, should be scrutinized to ensure that the part is compatible with the vehicle’s existing components. Verify the part’s compatibility with the vehicle’s existing components to avoid unforeseen issues.
Example Performance Part Compatibility Table
The following table provides an example of performance part compatibility with different vehicle models. Note that this is a simplified example, and comprehensive compatibility information should always be obtained from the part manufacturer or reputable online resources.
Vehicle Model | Performance Part | Compatibility |
---|---|---|
2023 Honda Civic | High-Flow Intake Manifold | Compatible (with necessary modifications for air intake system) |
2023 Honda Civic | Performance Exhaust System | Compatible (with proper exhaust hangers and clamps) |
2023 Toyota Camry | High-Flow Intake Manifold | Not Compatible |
2023 Toyota Camry | Performance Exhaust System | Compatible (with necessary modifications) |
Performance Part Market Trends and Developments
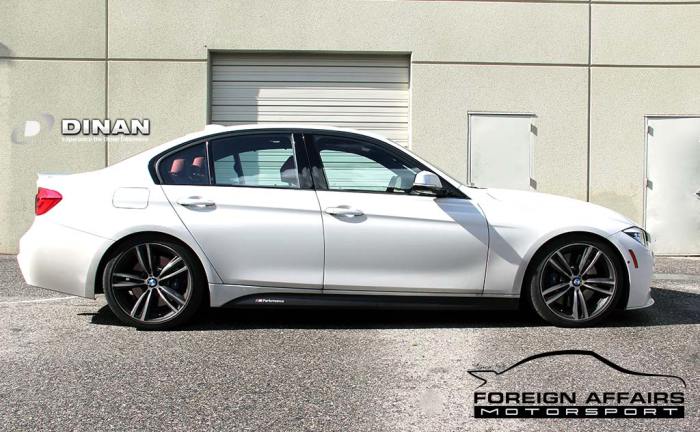
The performance parts market is dynamic, driven by advancements in materials science, engineering design, and evolving consumer preferences. This sector consistently adapts to meet the demands of enthusiasts and professionals seeking enhanced performance in various applications. Understanding the current trends and emerging technologies is crucial for businesses involved in the development, production, and sale of performance parts.
Current Trends
The performance parts market exhibits several key trends. Growing consumer demand for high-performance vehicles, combined with an increasing focus on sustainability, is influencing the market. Emphasis is being placed on lightweight materials, reduced emissions, and improved fuel efficiency. This translates to innovative designs and materials in performance parts, driving the evolution of the market. Moreover, technological advancements in data analytics and performance monitoring are leading to more precise tuning and optimization strategies for performance parts.
The rising popularity of aftermarket parts and customization further fuels the demand for performance enhancements.
Emerging Technologies
The introduction of new materials and manufacturing techniques is reshaping the landscape of performance parts. Advanced composites, such as carbon fiber and high-strength polymers, are increasingly used to create lighter and stronger components. Additive manufacturing (3D printing) is enabling the creation of complex geometries and personalized parts, providing significant advantages in terms of design flexibility and production efficiency.
These advancements result in improved performance, reduced manufacturing costs, and enhanced customization options for consumers.
Innovations in Performance Part Design
Modern performance parts often incorporate advanced design features. Aerodynamic enhancements, such as optimized air intakes and spoilers, contribute to increased efficiency and reduced drag. Sophisticated cooling systems, incorporating advanced materials and fluid dynamics principles, enhance the longevity and performance of components under high-stress conditions. The integration of electronic controls and sensors allows for dynamic adjustments to parameters such as engine power and suspension settings, maximizing performance and handling characteristics.
New Performance Parts and Applications
Examples of innovative performance parts include lightweight carbon fiber intake manifolds for enhanced engine breathing, titanium exhaust systems for improved exhaust flow, and advanced clutch kits designed for high-performance applications. These parts find applications in a wide range of vehicles, from high-performance sports cars to off-road trucks and racing motorcycles. The adoption of these components is rapidly increasing in motorsport and high-performance automotive applications.
Growth Potential
The performance parts market demonstrates substantial growth potential, driven by factors such as the expansion of the high-performance vehicle market and the increasing demand for customization. Technological advancements, coupled with a growing awareness of performance enhancement, are fueling the continued expansion of this market segment. The global demand for performance-oriented products in various sectors, such as aviation and industrial machinery, further contributes to the market’s projected growth.
Performance Part Performance Testing and Validation
Thorough testing and validation are crucial for ensuring performance parts meet expected specifications and deliver the promised benefits. This process involves rigorous evaluation methods to confirm functionality, reliability, and safety. A well-defined testing strategy safeguards against unforeseen issues and builds confidence in the part’s suitability for its intended application.
Methods for Testing Performance Part Functionality
Testing performance parts requires a systematic approach that encompasses various methodologies. Different testing methods are tailored to assess specific aspects of performance, such as durability, speed, efficiency, and safety. The choice of method hinges on the characteristics of the part and the performance metrics being evaluated.
- Load Testing: This method subjects the performance part to progressively increasing loads to determine its capacity and stress limits. It’s vital in evaluating the part’s ability to withstand operational demands without failure. For example, a suspension component might be subjected to simulated road conditions, including varying weights and bumps, to identify its maximum load-bearing capacity.
- Endurance Testing: This type of testing evaluates the performance part’s ability to withstand repeated cycles of operation over an extended period. It determines the part’s long-term reliability and durability. For instance, a motor component could be cycled thousands of times to assess its ability to maintain performance under continuous use.
- Environmental Testing: This method assesses the performance part’s resilience to environmental factors, such as temperature fluctuations, humidity, and exposure to chemicals. It’s essential to verify that the part can function effectively under diverse operational conditions. For example, a component designed for outdoor use might be tested in extreme temperatures or subjected to saltwater spray to ensure its resistance.
Validation of Performance Part Effectiveness
Validation involves confirming that the performance part meets the defined specifications and delivers the intended performance benefits. This process typically involves comparing test results against pre-determined criteria and benchmarks. Rigorous validation ensures that the part performs as expected and meets the requirements of its intended application.
- Statistical Analysis: Data collected during testing is analyzed statistically to identify trends and patterns. This allows for objective evaluation of the part’s performance and consistency. Statistical analysis can highlight any deviations from the expected performance, aiding in the identification of potential issues.
- Comparison with Standards: Validation also involves comparing the performance part’s results against industry standards or predefined specifications. Adherence to these standards guarantees that the part meets the requisite quality and safety requirements. For instance, a component for automotive use might be compared to SAE standards to ensure compliance.
- Field Trials: In some cases, field trials are employed to evaluate the performance part’s real-world performance. This method allows for testing under realistic conditions and provides valuable insights into the part’s practical effectiveness. This approach helps to validate performance in diverse operating conditions and applications.
Importance of Rigorous Testing Procedures
Rigorous testing procedures are essential for minimizing risks and ensuring quality. They provide a systematic approach to evaluating performance parts and confirm that they meet the required standards. Robust testing processes reduce the likelihood of defects or failures in the field, safeguarding the safety and reliability of the system.
Comparison of Performance Part Testing Methods
Testing Method | Description | Strengths | Weaknesses |
---|---|---|---|
Load Testing | Evaluates part’s strength and capacity under increasing loads. | Identifies stress limits, crucial for durability. | May not fully capture long-term effects. |
Endurance Testing | Assesses part’s performance over repeated cycles. | Provides insights into long-term reliability. | Can be time-consuming and expensive. |
Environmental Testing | Evaluates part’s performance in diverse environmental conditions. | Identifies part’s resilience to various factors. | Complex setups, requiring specialized equipment. |
Performance Part Safety Considerations
Ensuring the safe operation and longevity of any system, especially those involving mechanical or performance-enhancing modifications, requires meticulous attention to safety considerations. Improper installation or use of performance parts can lead to significant risks and potential harm. This section will explore the crucial aspects of safety associated with performance parts, emphasizing the importance of adhering to manufacturer guidelines and understanding the potential hazards.Performance part modifications, while potentially improving system performance, often introduce new safety challenges.
A thorough understanding of these considerations is paramount for avoiding accidents and maintaining a safe operating environment.
Safety Implications of Installation
Installation of performance parts necessitates careful consideration of potential safety risks. Neglecting proper installation procedures can compromise the integrity of the system, potentially leading to failure and catastrophic consequences. Improperly installed components can result in weakened structural integrity, increased stress on critical systems, and reduced safety margins. Understanding the specific implications of each modification is crucial for mitigating potential hazards.
Adherence to Manufacturer Guidelines
Manufacturer guidelines provide critical information regarding safe installation, operation, and maintenance procedures for performance parts. These guidelines are meticulously developed to ensure optimal performance while minimizing risks. Carefully following these instructions is paramount for maintaining safety and avoiding unforeseen consequences. These guidelines often detail specific torque specifications, component compatibility, and operational limits. Deviations from these guidelines can lead to catastrophic failures, necessitating a comprehensive understanding of the provided instructions.
Risks of Improper Installation or Use
Improper installation or use of performance parts can have severe safety consequences. Examples include component failure, system malfunction, and potential injury to the user or bystanders. The risks associated with improper installation or use are significant and often directly correlated to the extent of the deviation from manufacturer guidelines. For instance, using an incorrectly sized or incompatible part can lead to excessive stress on other components, potentially causing fractures or structural damage.
Potential Hazards and Mitigation Strategies
Various potential hazards are associated with performance part modifications. These hazards may include, but are not limited to, component failure, system instability, and elevated operational temperatures. The potential for injury from flying debris or unexpected system failure is another concern. Implementing mitigation strategies is crucial for minimizing these risks. These strategies often include rigorous testing protocols, careful component selection, and adherence to stringent installation procedures.
Properly designed safety features, such as reinforced mounting brackets or heat dissipation systems, can also play a vital role in mitigating potential hazards. Regular inspection and maintenance, as Artikeld by the manufacturer, can help identify and address potential issues before they escalate into safety hazards. For instance, monitoring fluid levels and temperatures in performance-modified engines is crucial to prevent overheating and potential fires.
Importance of Thorough Testing and Validation
Thorough testing and validation are essential to ensure that performance parts meet safety standards and are compatible with the existing system. This validation process typically includes rigorous simulations, component stress tests, and real-world trials. These tests help identify potential weaknesses and vulnerabilities, allowing for the development of mitigation strategies. Comprehensive validation procedures are critical to ensuring the safety of the system.
Performance Part Cost and Value Proposition
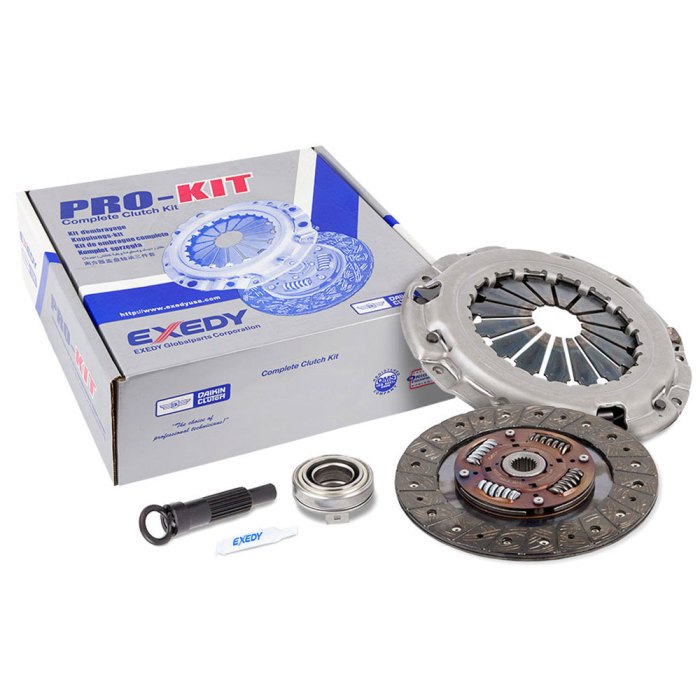
Performance part pricing strategies are crucial for both manufacturers and consumers. Understanding the cost structure and value proposition is essential for informed decisions regarding upgrades and replacements. This section details pricing strategies, compares costs to standard parts, analyzes the cost-benefit ratio, and presents diverse pricing models.Pricing strategies for performance parts are often complex, encompassing various factors that influence the final price.
These factors include material costs, manufacturing processes, research and development expenses, design and engineering complexities, marketing and branding, and profit margins. Ultimately, a balance between affordability and the perceived value of the enhanced performance must be struck.
Pricing Strategies for Performance Parts
Various pricing strategies are employed for performance parts. Often, performance parts command a premium over standard parts due to their enhanced features and performance characteristics. A common approach is premium pricing based on perceived value, reflecting the benefits gained. Volume discounts or tiered pricing can be offered to incentivize larger purchases. Special promotions or seasonal discounts can also be implemented to attract customers.
Cost Comparison with Standard Parts
Performance parts frequently come at a higher cost than their standard counterparts. This premium is often justified by the improved performance, efficiency, and longevity that these parts offer. A direct comparison of the materials, manufacturing processes, and features between standard and performance parts reveals the reasons for the price disparity. The enhanced components and superior design are usually reflected in the increased cost.
Cost-Benefit Analysis
The cost-benefit analysis of performance parts evaluates the return on investment. This assessment weighs the cost of the part against the expected performance gains, operational efficiency, and longevity. Factors such as fuel economy improvements, reduced maintenance costs, and enhanced safety features should be considered. By evaluating these benefits against the price, the potential return on investment becomes clear.
For instance, a performance exhaust system may cost more upfront but offer improved fuel efficiency and a more enjoyable driving experience, justifying the cost over the vehicle’s lifespan.
Pricing Models for Performance Parts
Different pricing models are employed for various performance parts. For example, a performance air intake may be priced based on its filtration system’s efficiency and materials, whereas a high-performance clutch might be priced based on its durability and component specifications. OEM (Original Equipment Manufacturer) parts are often priced based on standard market value. Alternatively, aftermarket performance parts might use a tiered pricing structure based on performance level, materials, or features.
Performance Part | Pricing Model | Justification |
---|---|---|
Performance Exhaust System | Premium Pricing | Improved sound and performance |
Performance Suspension Components | Tiered Pricing | Varying spring rates and damper adjustments |
Performance Brake Kits | Value-Based Pricing | Increased stopping power and durability |
Final Wrap-Up
In conclusion, performance parts are a multifaceted area that encompasses a broad spectrum of options for enhancing vehicle performance and handling. Understanding the diverse range of parts, their benefits and drawbacks, proper installation and maintenance, and the safety considerations is crucial for any enthusiast. By carefully considering these factors, you can make informed decisions that align with your vehicle’s needs and personal preferences.
Quick FAQs
What are the common materials used in performance parts?
Performance parts often utilize high-strength alloys like aluminum, steel, and titanium, alongside composites for enhanced durability and lightness. Specific material choices depend on the part’s function and the desired performance characteristics.
What are the potential risks of improper installation?
Improper installation can lead to reduced performance, safety hazards, and potential damage to the vehicle’s components. It’s crucial to follow manufacturer guidelines and consult professionals for accurate installation.
How can I determine the compatibility of a performance part with my vehicle?
Always check the part number and specifications against your vehicle’s make, model, and year. Refer to the manufacturer’s compatibility charts or consult a knowledgeable mechanic to ensure proper fitment.
What are some common performance part testing methods?
Testing methods vary but may include dynamometer testing to measure horsepower and torque output, track testing to evaluate handling and acceleration, and road-based evaluations to assess real-world performance.