Engine diagnostics is a crucial aspect of maintaining and optimizing engine performance across various industries. From basic visual inspections to advanced techniques like vibration analysis, understanding the intricacies of engine diagnostics is essential for preventing costly repairs and maximizing efficiency. This guide explores the full spectrum of engine diagnostics, from fundamental principles to cutting-edge advancements.
This in-depth exploration covers everything from the historical evolution of diagnostic tools to the interpretation of complex data. We’ll delve into common diagnostic procedures, troubleshoot various engine problems, and examine the unique applications of engine diagnostics in diverse industries, including automotive, industrial, marine, and aviation sectors. The content includes detailed explanations, practical examples, and a comparison of different diagnostic methods to help you gain a comprehensive understanding of the subject.
Introduction to Engine Diagnostics
Engine diagnostics is the systematic process of identifying and analyzing malfunctions within an engine’s operational components. This process is crucial for maintaining optimal performance, preventing costly repairs, and ensuring safety in various applications. Accurate diagnosis minimizes downtime and maximizes efficiency.Accurate engine diagnostics are essential for a wide range of applications, from automotive vehicles to industrial machinery. Proper diagnosis allows for timely intervention, preventing further damage and potential hazards.
Early identification of issues often translates to significant cost savings compared to addressing problems after they escalate. This is particularly important in industrial settings where equipment downtime can severely impact productivity and profitability.
Engine Diagnostic Methods
A variety of techniques are employed in engine diagnostics. These methods range from simple visual inspections to complex mechanical and electronic testing procedures. The choice of method depends on the suspected issue and the available resources.
Types of Engine Diagnostics
Different types of diagnostics exist, each with its own set of advantages and limitations. A comprehensive diagnostic approach often involves a combination of these methods to achieve the most accurate results.
Method | Advantages | Disadvantages | Applications |
---|---|---|---|
Visual Inspection | Simple, inexpensive, readily available, identifies obvious issues like leaks, loose components, and visible damage. | Limited to surface-level issues, cannot detect internal problems, requires trained personnel for accurate assessment. | Preliminary checks, basic maintenance, troubleshooting simple malfunctions, assessing damage after accidents. |
Mechanical Testing | Directly assesses the mechanical function of components, can reveal issues like misalignment, wear, and lubrication problems. | Can be time-consuming, requires specialized tools and equipment, may not pinpoint the exact cause of a problem. | Assessing engine performance (e.g., compression tests), verifying component functionality, checking for leaks and pressure issues. |
Electronic Testing | Identifies electronic malfunctions and system issues, often provides detailed diagnostic codes and information about the problem. | Requires specialized equipment, knowledge of diagnostic tools and systems, may require specialized personnel for effective implementation. | Modern vehicles, complex machinery with electronic control systems, identifying specific sensor or control module failures. |
Historical Evolution of Diagnostic Tools and Techniques
Engine diagnostics has evolved significantly over time, moving from rudimentary visual inspections to sophisticated electronic analyses. Early methods relied heavily on visual observation and basic mechanical tests. The introduction of electronic control units (ECUs) in modern engines necessitated the development of specialized diagnostic tools and techniques to interpret the data generated by these systems. This evolution has led to faster, more accurate, and more comprehensive diagnoses.
Diagnostic Tools and Equipment
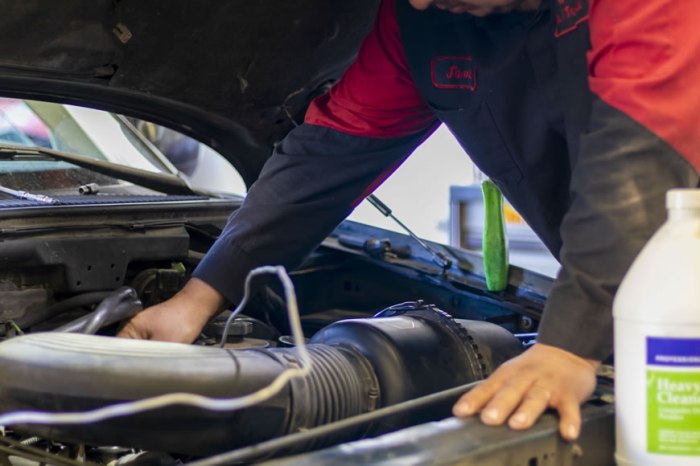
Engine diagnostics relies heavily on a variety of specialized tools and equipment to accurately identify and address issues. These tools provide critical insights into the engine’s performance, allowing technicians to pinpoint problems with efficiency and precision. Proper selection and use of these tools are essential for effective and timely repairs.
Common Diagnostic Tools
Various tools aid in engine diagnostics, each with specific functionalities. These tools are crucial for pinpointing problems, and the appropriate tool selection depends on the specific issue being investigated. Engine analyzers, oscilloscopes, and sensors are key components in this process.
Engine Analyzers
Engine analyzers are sophisticated instruments that collect and process data from various engine components. They provide a comprehensive overview of engine performance parameters, enabling technicians to identify potential malfunctions quickly. Data collected often includes engine speed, fuel consumption, exhaust emissions, and sensor readings. Engine analyzers allow for detailed analysis and often feature built-in diagnostic software for easy interpretation of results.
For example, a malfunctioning ignition system might show up as erratic spark timing or abnormal voltage fluctuations in the analyzer’s output.
Oscilloscopes
Oscilloscopes are valuable tools for visualizing electrical waveforms. They capture and display voltage and current signals from various engine components, providing a detailed view of their electrical activity. This visual representation is crucial for identifying erratic signals, voltage spikes, or other anomalies that might indicate a problem. For instance, an oscilloscope can capture the voltage signal from a crankshaft position sensor, enabling technicians to detect any issues with the signal’s shape or timing.
Sensors
Sensors are integral to engine diagnostics, providing real-time data about various engine parameters. These sensors convert physical phenomena, such as temperature, pressure, and position, into electrical signals that can be interpreted by diagnostic tools. Different sensors provide data on critical engine functions. For instance, oxygen sensors monitor air-fuel ratios, while crankshaft position sensors track engine speed and position.
- Oxygen Sensors: These sensors measure the amount of oxygen in the exhaust gases, providing crucial data for optimizing fuel combustion and emission control. Variations from the expected readings can signal issues with the fuel system or catalytic converter.
- Crankshaft Position Sensors: These sensors track the position and rotation of the crankshaft, providing essential data for the engine control unit (ECU) to regulate ignition timing and fuel delivery. A faulty sensor can lead to erratic engine performance.
- Throttle Position Sensors: These sensors measure the position of the throttle plate, relaying this information to the ECU for adjusting fuel delivery and air intake according to the driver’s input. Malfunctioning sensors can result in inaccurate engine response to throttle commands.
Data Acquisition Systems
Data acquisition systems are essential for gathering and recording sensor data from various engine components. These systems play a vital role in engine diagnostics by providing a centralized repository of information. The collected data can then be analyzed by diagnostic tools, offering comprehensive insights into the engine’s performance and health. Modern systems often integrate with engine analyzers and computers, facilitating data analysis and report generation.
Typical Workflow of Using an Engine Analyzer
- Connection: Connect the engine analyzer to the vehicle’s diagnostic ports, ensuring proper connections are established.
- Data Acquisition: Initiate data acquisition from the engine, capturing data on relevant parameters such as engine speed, fuel consumption, and sensor readings.
- Analysis: Analyze the collected data to identify any anomalies or deviations from expected values. Software on the analyzer will help to determine any deviations from normal operating conditions.
- Reporting: Generate a report detailing the analysis results, highlighting any detected issues or potential problems.
Diagnostic Procedures and Techniques
Engine diagnostics often involves a systematic approach to identify and resolve issues. This involves employing various procedures and techniques, ranging from basic visual inspections to advanced diagnostic tool applications. Understanding these procedures is crucial for effective troubleshooting and efficient repairs.
Common Diagnostic Procedures for Engine Problems
A range of diagnostic procedures is employed to address different engine issues. These procedures typically follow a systematic approach, moving from general checks to more specific analyses. The initial steps often involve a visual inspection and basic checks to identify the potential source of the problem.
- Misfiring: Misfiring issues often manifest as irregular engine operation, rough idling, and decreased power output. The diagnostic procedure typically begins with checking spark plug condition, fuel delivery, and ignition system components. This may include verifying spark plug gap, inspecting fuel injectors for clogs, and ensuring proper ignition timing. Further checks may include evaluating air intake and exhaust system conditions.
If the issue persists, a detailed analysis of the engine’s sensor readings, such as crankshaft position sensor and camshaft position sensor, is recommended. Example: A misfiring cylinder can be identified by uneven power output during acceleration or a noticeable stutter in the engine’s performance.
- Overheating: Overheating problems frequently result from insufficient coolant flow or inadequate cooling system function. The procedure starts with checking the coolant level and its condition. Next, the radiator and hoses are visually inspected for leaks or blockages. Thereafter, the thermostat and water pump are evaluated. Subsequent steps may include checking for air pockets in the cooling system and ensuring the fan is functioning correctly.
Example: A faulty thermostat can prevent the engine from reaching the optimal operating temperature, causing overheating under heavy load conditions.
- Low Power: Reduced engine power can be caused by various issues, from fuel delivery problems to air intake restrictions. The diagnostic process often begins with checking the fuel pressure and the air filter condition. This includes checking fuel pressure and fuel injector functionality, ensuring correct air intake, and inspecting the exhaust system for blockages. If the issue persists, the spark plugs, ignition coils, and oxygen sensor are evaluated.
Example: A clogged air filter restricts airflow, reducing the engine’s ability to properly combust the fuel-air mixture, leading to diminished power output.
Methods for Identifying and Isolating Faults
Effective fault isolation relies on systematic checks and tests. Several methods are used to pinpoint the exact cause of the engine problem.
- Visual Inspection: Visual checks are an initial diagnostic step. Inspecting components like hoses, belts, and connections can reveal potential problems such as leaks or damage. This can lead to the isolation of specific parts or systems.
- Component Testing: Direct testing of engine components, such as fuel injectors, spark plugs, and sensors, helps identify malfunctions. This often involves using diagnostic tools and procedures to assess their functionality. Example: A fuel injector test can help determine if the injector is delivering fuel at the correct pressure and quantity.
- System-Level Analysis: System-level analysis is an advanced diagnostic method. It involves evaluating the entire engine system to determine the relationship between different components. This may require using sophisticated diagnostic equipment to gather data and pinpoint the problem area. This is often followed by a systematic troubleshooting approach.
Safety Precautions During Engine Diagnostics
Adhering to safety precautions is crucial during engine diagnostics to prevent injuries or damage.
- Electrical Safety: Always disconnect the battery before working on any electrical components to avoid electrical shock. This is a crucial safety step to prevent any accidental electrical hazard.
- Hot Components: Allow hot components to cool down before handling them. Engine parts can become extremely hot during operation, causing burns if handled improperly. It’s critical to avoid touching any component until it is adequately cooled down.
- Tools and Equipment: Use appropriate tools and equipment for engine diagnostics. Incorrect tools can cause damage to components. This ensures the accuracy and precision of the diagnosis.
Interpreting Diagnostic Data
Interpreting the data generated by diagnostic tools is crucial for accurate engine problem identification. This involves understanding the various formats, codes, and messages presented by the tools, and correlating the information from different sensors to pinpoint the root cause of any issues. Correct interpretation is essential for efficient troubleshooting and effective repair.Effective analysis of engine performance data relies on recognizing patterns and trends within the generated graphs and charts.
Understanding how various parameters interact and affect each other is key to identifying potential problems. This approach helps in diagnosing malfunctions that might not be immediately apparent from a single data point.
Engine diagnostics is crucial for maintaining optimal vehicle performance. Understanding how different components interact within vehicles is key to accurate diagnoses. Proper diagnostics ensures the longevity and efficiency of your engine.
Analyzing Engine Performance Data
Engine performance data, often displayed graphically, provides valuable insights into the engine’s operational state. Graphs depicting parameters like fuel consumption, RPM, temperature, and pressure fluctuations can reveal anomalies and trends that signal potential issues. Careful examination of these graphical representations allows for the detection of irregularities in the engine’s behavior, which can indicate problems like misfires, fuel delivery issues, or cooling system malfunctions.
For instance, a sudden spike in exhaust temperature accompanied by a drop in fuel efficiency could point towards a problem with the combustion process.
Understanding Diagnostic Codes and Error Messages, Engine diagnostics
Diagnostic tools frequently generate codes and error messages to communicate specific issues. These codes, often in the form of alphanumeric strings, correspond to particular faults or malfunctions. Properly interpreting these codes is essential for effective troubleshooting. For example, a code like P0123 might indicate a problem with the engine’s throttle position sensor. Each code is associated with a specific component or system within the engine.
A thorough understanding of these codes allows for a focused approach to identifying the precise location of the malfunction.
Correlating Data from Different Sensors
Diagnosing complex engine problems often requires correlating data from multiple sensors. This approach allows for a comprehensive understanding of the engine’s overall operational state. For example, comparing data from the crankshaft position sensor with data from the oxygen sensor can reveal issues with ignition timing or fuel mixture. By combining insights from various sensors, a clearer picture of the problem emerges, leading to more precise diagnoses.
Table of Common Error Codes
Error Code | Description | Possible Causes | Troubleshooting Steps |
---|---|---|---|
P0123 | Throttle Position Sensor Circuit Malfunction | Faulty throttle position sensor, wiring problems, or damaged connectors | Inspect throttle position sensor, check wiring for continuity and damage, replace the sensor if necessary. |
P0300 | Random/Multiple Cylinder Misfire | Spark plug issues, fuel delivery problems, or ignition coil malfunction | Check spark plug condition, inspect fuel injectors, test ignition coils, and replace components as needed. |
P0420 | Catalyst System Efficiency Below Threshold (Bank 1) | Clogged or damaged catalytic converter, malfunctioning oxygen sensor, or insufficient fuel mixture | Inspect the catalytic converter, test the oxygen sensor, check for fuel mixture problems, and replace parts as required. |
Engine Fault Diagnosis
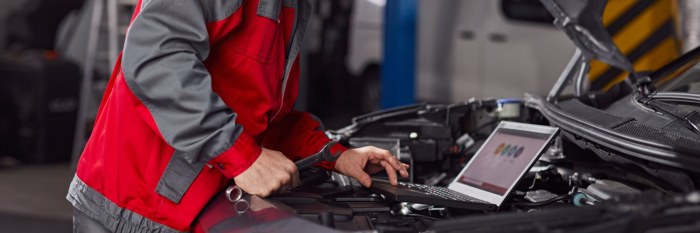
Engine fault diagnosis is a critical aspect of maintaining optimal engine performance and longevity. Accurate identification of faults is essential for timely repairs, preventing further damage, and minimizing downtime. This section delves into common engine faults, their causes, symptoms, and the importance of accurate diagnosis. Different diagnostic approaches are also discussed.
Common Engine Faults
Understanding common engine faults allows for proactive maintenance and faster resolution of issues. Knowing the typical symptoms and causes of these problems empowers technicians to effectively diagnose and repair them.
- Fuel System Malfunctions: Fuel delivery issues are prevalent, ranging from fuel pump failures to clogged fuel filters. These problems often manifest as erratic engine performance, difficulty starting, or complete engine shutdown. Proper diagnosis involves checking fuel pressure, fuel flow, and fuel filter condition. Inaccurate diagnosis can lead to unnecessary replacement of components and cost escalation.
- Ignition System Problems: Malfunctioning ignition components, such as spark plugs, coils, or the ignition control module, can lead to misfires, rough idling, or engine stalling. Troubleshooting involves checking spark plug condition, coil resistance, and ignition timing. Incorrectly diagnosing these issues can result in premature replacement of ignition parts.
- Exhaust System Leaks: Leaks in the exhaust system can cause decreased engine power, backpressure, and exhaust emissions violations. Symptoms include unusual exhaust noises, low power, and excessive smoke. Diagnosing these issues necessitates a visual inspection of the exhaust system for leaks, cracks, or damage.
- Cooling System Failures: Problems in the cooling system, including leaks, insufficient coolant, or radiator failures, can lead to overheating and potential engine damage. Identifying overheating problems requires careful monitoring of coolant temperature, checking for leaks, and inspecting the radiator. Incorrect diagnosis can lead to further engine damage if overheating is not addressed promptly.
- Electrical System Malfunctions: Electrical problems can cause numerous issues, such as sensor malfunctions, wiring problems, or faulty components. These problems often manifest as intermittent engine performance issues, warning lights, or complete system failure. Diagnostics involve checking wiring, connections, and the integrity of electrical components. Incorrect diagnosis of electrical problems can lead to unnecessary replacement of parts and wasted time.
Causes of Engine Faults
Understanding the root causes of engine faults aids in preventing recurring issues. Identifying the precise cause allows for targeted repairs and improved preventative maintenance.
- Fuel System Causes: Fuel pump failures, clogged fuel filters, and low fuel pressure can all lead to fuel delivery issues. Poor fuel quality, incorrect fuel ratios, and inadequate fuel pressure regulation can also contribute.
- Ignition System Causes: Damaged or worn spark plugs, faulty ignition coils, and incorrect ignition timing can all result in misfires and poor engine performance. Faulty ignition control modules can also disrupt the ignition sequence.
- Exhaust System Causes: Exhaust leaks are often caused by corrosion, damage from impact, or improper exhaust system installation. Leaks can also be caused by worn gaskets or faulty clamps.
- Cooling System Causes: Cooling system leaks, inadequate coolant levels, or damaged radiators are common causes of overheating. Poor coolant quality, or inadequate fan operation can also contribute.
- Electrical System Causes: Wiring problems, loose connections, faulty sensors, and component failures can all cause electrical system malfunctions. Overuse of electrical components or incorrect installation can also contribute to these issues.
Symptoms of Engine Faults
Recognizing the symptoms associated with engine faults is crucial for early detection and intervention. Prompt identification of symptoms enables timely diagnosis and prevents escalating problems.
- Fuel System Symptoms: Erratic engine performance, difficulty starting, rough idling, and complete engine shutdown are all indicators of fuel system problems.
- Ignition System Symptoms: Misfires, rough idling, stalling, and poor acceleration can be signs of ignition system problems.
- Exhaust System Symptoms: Unusual exhaust noises, low engine power, and excessive smoke are potential indicators of exhaust system leaks.
- Cooling System Symptoms: Overheating, excessive steam from the engine compartment, and low coolant levels are common symptoms of cooling system failures.
- Electrical System Symptoms: Intermittent engine performance issues, warning lights, and complete system failure are common symptoms of electrical system malfunctions.
Importance of Accurate Fault Identification
Accurate fault identification is paramount for effective repairs and prevents further damage. A precise diagnosis minimizes downtime, cost, and the risk of recurring issues.
Diagnostic Approaches
Various diagnostic approaches exist, each with advantages and limitations. Choosing the appropriate method for a specific fault is critical for efficient troubleshooting.
- Visual Inspection: Visual inspection is a fundamental step in many diagnostics. This approach involves a careful examination of visible components for damage, leaks, or unusual wear. This initial step can quickly identify many potential problems.
- Scanning Tools: Advanced diagnostic tools, such as scan tools, can retrieve fault codes and provide insights into system functionality. This approach allows for quicker identification of the precise nature of the fault. However, the use of scan tools requires understanding of the specific fault codes.
- Component Testing: Testing specific components, like fuel injectors or sensors, allows for a more focused approach. Testing involves applying appropriate tests and procedures to verify the proper functionality of individual parts.
Advanced Diagnostic Techniques: Engine Diagnostics
Advanced diagnostic techniques are crucial for pinpointing the root cause of complex engine issues that standard diagnostic procedures might miss. These methods often involve specialized equipment and data analysis, allowing for a more thorough understanding of engine operation and identifying subtle anomalies. These techniques are particularly valuable in situations where the problem isn’t immediately apparent or involves intricate interactions within the engine system.Advanced techniques often involve sophisticated data acquisition and analysis.
This is crucial as it can identify patterns and trends in the data that may not be immediately obvious to the naked eye. This detailed analysis can lead to a more precise diagnosis and, ultimately, a more effective repair.
Vibration Analysis
Vibration analysis is a valuable tool for identifying mechanical issues within an engine. This technique involves monitoring the vibrations of various engine components. Sophisticated sensors capture these vibrations, which are then processed to identify patterns and anomalies.Vibration analysis is particularly effective in detecting issues like misalignment, bearing wear, or imbalance in rotating parts. This data can provide insight into the health of crucial components like crankshafts, connecting rods, and other moving parts.
Engine diagnostics are crucial for any car owner. Properly understanding your engine’s health is a key aspect of preventative car maintenance, like checking fluid levels and tire pressure. A good understanding of car maintenance practices will help you catch potential problems early, ultimately saving you money and hassle down the road. This, in turn, ensures that your engine runs smoothly and efficiently for a longer time.
Early detection of these issues is critical to preventing catastrophic failures and costly repairs. For example, a sudden increase in vibration frequency might indicate a damaged crankshaft bearing. Consistent high-frequency vibrations might suggest a misaligned component.
Emission Testing
Emission testing is essential for evaluating the exhaust emissions of an engine. This technique is employed to determine if the engine is functioning within acceptable environmental limits. Specialized equipment measures the concentration of various pollutants in the exhaust stream. Modern techniques often involve sophisticated gas analyzers and advanced data acquisition systems.This process is vital in identifying problems related to fuel injection, combustion, or catalytic converter efficiency.
For instance, an unusually high concentration of hydrocarbons in the exhaust could suggest a malfunction in the fuel system. Monitoring emissions is crucial for adhering to environmental regulations and ensuring the engine is operating cleanly and efficiently.
Data Analysis in Advanced Techniques
Data analysis plays a pivotal role in extracting meaningful information from advanced diagnostic techniques. This involves utilizing various analytical methods, including statistical analysis and pattern recognition. Sophisticated software tools are often employed to process and interpret the vast amount of data generated during these procedures.Accurate interpretation of data is crucial. Errors in analysis can lead to incorrect diagnoses, resulting in unnecessary repairs or a delay in identifying the actual problem.
Furthermore, detailed analysis can reveal subtle trends in the data that may not be immediately apparent, leading to a more precise understanding of the underlying issue.
Comparison of Advanced Techniques
Technique | Pros | Cons | Applications |
---|---|---|---|
Vibration Analysis | Early detection of mechanical issues, detailed insight into component health, relatively non-invasive. | Requires specialized equipment, data interpretation can be complex, may not always pinpoint the exact cause. | Identifying misalignment, bearing wear, imbalance in rotating parts, assessing overall engine health. |
Emission Testing | Compliance with environmental regulations, identification of combustion issues, objective assessment of engine performance. | Can be time-consuming, may not always directly reveal internal component issues, expensive equipment required. | Evaluating exhaust emissions, determining fuel system efficiency, ensuring adherence to environmental standards. |
Engine Maintenance and Repair
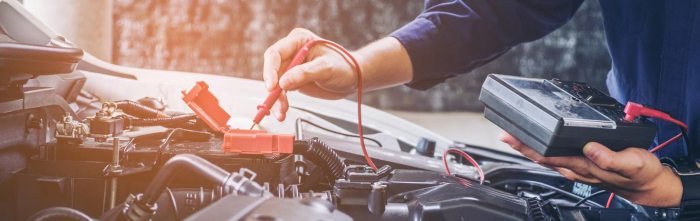
Engine diagnostics and maintenance are intrinsically linked. Effective maintenance significantly reduces the need for costly repairs and extends the lifespan of the engine. Proper maintenance, coupled with timely diagnostics, allows for proactive identification and resolution of potential issues before they escalate into major problems.Engine diagnostics play a critical role in guiding repair decisions. By pinpointing the root cause of a malfunction, diagnostics provide a precise understanding of the necessary repairs, minimizing guesswork and ensuring the correct components are replaced.
This targeted approach is more efficient and economical compared to performing a general repair, which may not address the actual problem.
Connection Between Diagnostics and Maintenance
Regular maintenance procedures, such as oil changes, filter replacements, and inspections, are crucial in preventing future engine problems. These preventative measures help maintain optimal engine performance and longevity. Diagnostics are vital in determining the efficacy of these maintenance tasks. For instance, a diagnostic check after an oil change can confirm the proper oil level and quality, and the effectiveness of the filter replacement.
Regularly scheduled maintenance, combined with diagnostic monitoring, creates a proactive maintenance strategy.
Routine Engine Maintenance Recommendations
Maintaining a well-maintained engine involves adhering to a scheduled maintenance routine. This includes tasks like:
- Oil Changes: Changing the engine oil at the recommended intervals is essential for lubrication and preventing wear. This prevents buildup of contaminants and ensures consistent lubrication, crucial for engine health.
- Filter Replacements: Regular replacement of air, fuel, and oil filters is vital. Clogged filters restrict airflow, fuel delivery, and oil circulation, leading to decreased engine performance and increased wear.
- Fluid Checks: Ensuring adequate levels of coolant, brake fluid, and power steering fluid is crucial. Insufficient levels can lead to overheating, brake failure, and steering issues.
- Visual Inspections: Regular visual checks for leaks, unusual noises, or damage are vital. Early detection of problems often prevents them from escalating into more significant issues.
- Component Inspection: Inspecting belts, hoses, and other critical components can reveal potential issues before they cause major problems.
Role of Diagnostics in Repair Decisions
Engine diagnostics are indispensable in guiding repair decisions. Diagnostic tools provide detailed information about the specific components and systems involved in a malfunction. This enables technicians to pinpoint the root cause, rather than guessing or performing general repairs. A diagnostic report aids in accurately determining the required repair procedures and the specific parts that need replacement. For example, a diagnostic code might indicate a faulty sensor, necessitating only sensor replacement rather than a more extensive repair.
Applying Diagnostic Findings to Repair Procedures
Diagnostic data is directly applied to repair procedures. For instance, if a diagnostic scan reveals a misfire in cylinder 3, the technician can focus on the components associated with that cylinder. This targeted approach saves time and resources, preventing unnecessary component replacements.
Replacing Spark Plugs (Example)
Replacing spark plugs, based on diagnostic results, involves several steps:
- Diagnostic Check: A diagnostic scan identifies a misfire in specific cylinders, indicating potential spark plug issues.
- Gathering Parts: The correct spark plugs are ordered, ensuring compatibility with the engine type.
- Engine Preparation: The engine is properly prepared for the replacement, including draining the coolant and lubricating the engine as needed.
- Spark Plug Removal: The old spark plugs are carefully removed using the appropriate tools. Proper removal prevents damage to the engine.
- Spark Plug Inspection: The removed spark plugs are inspected for signs of damage, wear, or excessive carbon buildup. This helps determine if other components need attention.
- New Spark Plug Installation: New spark plugs are installed in the correct orientation. Tightening them to the correct torque is critical to ensure proper functionality.
- Engine Reassembly: The engine is reassembled, ensuring all components are correctly positioned.
- Post-Repair Diagnostics: A final diagnostic scan confirms the successful repair, ensuring the problem is resolved.
Engine Diagnostics in Different Industries
Engine diagnostics plays a crucial role in maintaining optimal performance and safety across various industries. From ensuring reliable power generation to maintaining the integrity of marine vessels and aircraft, accurate engine diagnostics is vital for minimizing downtime, preventing catastrophic failures, and maximizing efficiency. Different industries present unique challenges and requirements for engine diagnostics, demanding specialized approaches and tailored solutions.
Marine Industry Applications
Engine diagnostics in the marine sector focuses on maintaining the integrity and efficiency of vessels, from large cargo ships to smaller recreational boats. The primary goal is to prevent breakdowns in critical environments and maintain safety for personnel and cargo. Engine failures in marine environments can have significant consequences, including delays, financial losses, and potential environmental hazards.
- Real-time monitoring of key parameters like vibration, temperature, and oil pressure is crucial for early detection of potential issues. This data is often collected and analyzed remotely to allow for proactive maintenance and prevent costly repairs at sea.
- Predictive maintenance is highly valued in marine operations. Algorithms analyze historical data and current conditions to predict potential failures, enabling preemptive maintenance and reducing unexpected downtime.
- Specialized diagnostic tools, often integrated with onboard systems, are essential for marine applications. These tools need to withstand harsh environments and be readily accessible to crew members.
Aviation Industry Applications
Engine diagnostics in aviation is paramount for ensuring the safety and reliability of aircraft. Engine failures in the air can have devastating consequences, necessitating a high degree of precision and proactive monitoring. Advanced diagnostic techniques are crucial for maintaining flight safety.
- Flight data recorders capture critical data about engine performance during flight, allowing for post-flight analysis and identification of potential problems. This data often involves intricate data analysis to pinpoint anomalies.
- Remote diagnostics through satellite communication enable real-time monitoring and analysis of engine performance even during extended flights.
- Engine health monitoring is constantly performed using sophisticated sensors and data analysis tools. These tools identify subtle deviations in engine performance, alerting technicians to potential problems before they become catastrophic.
Power Generation Industry Applications
Engine diagnostics in power generation is critical for maintaining the continuous operation of power plants. These facilities require high levels of reliability and dependability to provide electricity to consumers. Engine failures can disrupt power grids and cause significant financial losses.
- Continuous monitoring of engine parameters is vital for preventing sudden failures. Data analysis from sensors helps anticipate problems before they escalate.
- Predictive analytics are used to forecast maintenance needs and schedule repairs in advance. This approach optimizes maintenance schedules, minimizing downtime and maximizing plant efficiency.
- Customization is key in this sector. Power generation plants utilize a variety of engine types and sizes, requiring diagnostic solutions that cater to these specific requirements. This is crucial for optimizing the performance of specific engine models.
Customization and Industry-Specific Solutions
Diagnostic tools and procedures are often customized for each industry based on specific operating conditions, regulatory requirements, and environmental factors. Customization plays a critical role in ensuring that diagnostics are appropriate for the unique demands of each industry. This includes adapting diagnostic tools to specific engine types, developing industry-specific maintenance schedules, and incorporating safety protocols tailored to the environment.
Comparison of Engine Diagnostic Practices
Industry | Diagnostic Approach | Challenges | Tools |
---|---|---|---|
Marine | Real-time monitoring, predictive maintenance, specialized tools | Harsh environments, remote operation, safety concerns | Vibration sensors, pressure sensors, onboard diagnostic systems |
Aviation | Flight data recorders, remote diagnostics, continuous monitoring | Safety critical, high-speed operation, regulatory compliance | Engine health monitoring systems, flight data recorders, advanced sensors |
Power Generation | Continuous monitoring, predictive analytics, customized solutions | Continuous operation, high-load conditions, regulatory compliance | Advanced monitoring systems, predictive maintenance software, specialized sensors |
Future Trends in Engine Diagnostics
Engine diagnostics are constantly evolving, driven by the need for enhanced efficiency, safety, and reduced maintenance costs. Emerging technologies are transforming how we analyze engine performance and predict potential issues, paving the way for a more proactive and data-driven approach to maintenance.
AI-Powered Diagnostics
Artificial intelligence (AI) is rapidly integrating into engine diagnostics, enabling sophisticated pattern recognition and predictive capabilities. AI algorithms can analyze vast datasets of sensor data, identifying subtle anomalies that might be missed by traditional methods. This allows for early detection of potential failures, enabling preventative maintenance and minimizing downtime. The use of machine learning (ML) models allows for continuous improvement and adaptation to new operating conditions.
Predictive Maintenance
Predictive maintenance, enabled by AI and advanced data analytics, is transforming engine maintenance strategies. By analyzing sensor data, historical performance records, and environmental factors, predictive models can forecast potential failures before they occur. This approach allows for proactive maintenance schedules, reducing unscheduled downtime and increasing equipment lifespan. Examples of predictive maintenance in other industries show a significant reduction in maintenance costs and increased operational efficiency.
Data Analytics in Diagnostics
Data analytics plays a pivotal role in future diagnostic approaches. The sheer volume of data generated by modern engines demands sophisticated analytical techniques to extract meaningful insights. Statistical modeling, machine learning algorithms, and data visualization tools are critical for identifying patterns and correlations in sensor data, enabling proactive maintenance strategies. The insights gained from data analysis can be used to optimize engine design, improve operational efficiency, and reduce environmental impact.
Hypothetical Scenario: AI-Assisted Engine Diagnostics
Imagine a fleet of heavy-duty trucks. Each truck is equipped with a sophisticated sensor network monitoring various engine parameters. An AI system, trained on a vast dataset of historical engine performance and maintenance records, analyzes the real-time sensor data. If the system detects a pattern indicative of an impending bearing failure, it proactively alerts the maintenance team.
This allows for the timely replacement of the bearing, preventing catastrophic engine failure and costly repairs. The AI system can also identify optimal maintenance schedules for each truck based on its individual usage patterns, maximizing uptime and minimizing downtime. This approach is based on current technologies and has been successfully applied in various industries.
Last Word
In conclusion, engine diagnostics is a multifaceted field requiring a thorough understanding of both fundamental principles and advanced techniques. This comprehensive guide has provided a detailed overview of the process, equipping readers with the knowledge necessary to effectively diagnose and resolve engine issues. From basic inspections to advanced data analysis, the strategies presented offer a robust framework for optimizing engine performance and preventing costly failures across diverse industries.
The future of engine diagnostics promises exciting advancements, particularly with the integration of AI-powered systems, ensuring continued improvement in efficiency and safety.
FAQ Summary
What are some common symptoms of a misfiring engine?
Common symptoms include rough idling, erratic acceleration, and a noticeable “miss” or “knock” sound. The severity of these symptoms can vary depending on the extent of the misfire.
How can I interpret the error codes generated by diagnostic tools?
Diagnostic tools often generate error codes with specific descriptions and potential causes. Consulting a comprehensive reference table or manual is essential for accurate interpretation. Correlating data from multiple sensors is also vital for accurate diagnosis.
What are the safety precautions when performing engine diagnostics?
Always ensure the engine is properly shut down, disconnected from power sources, and cooled before any diagnostic procedures are performed. Use appropriate safety equipment, such as gloves and eye protection, to prevent potential hazards.
What is the role of data acquisition systems in engine diagnostics?
Data acquisition systems record and process the vast amounts of data generated by various sensors. This data is critical for identifying trends, patterns, and anomalies, ultimately enabling a more accurate and comprehensive diagnosis.