Vehicle recall sets the stage for a detailed exploration of the process, from initial defect identification to long-term impact. This involves understanding the intricacies of communication strategies, the financial ramifications for both manufacturers and consumers, and the crucial role of safety and quality control in preventing future issues.
This guide delves into the various aspects of vehicle recalls, offering insights into the legal frameworks, international variations, and the critical importance of customer support during such events. It examines case studies, both successful and unsuccessful, to highlight lessons learned and strategies for proactive recall prevention.
Vehicle Recall Overview
Vehicle recalls are a critical safety measure implemented by automotive manufacturers to address potential defects or hazards in their vehicles. These actions are essential for protecting public safety and maintaining consumer confidence in the quality and reliability of products. A comprehensive understanding of the recall process, types, and regulatory frameworks is crucial for consumers to navigate these situations effectively.The process of a vehicle recall involves several steps, from identifying a potential defect to notifying affected owners and providing corrective actions.
Manufacturers use various methods to reach vehicle owners, including mail, online portals, and potentially even SMS or email campaigns, depending on the specifics of the situation and the scale of the recall.
Purpose and Process of Vehicle Recalls
Vehicle recalls are initiated to rectify safety-related issues that may pose a risk to vehicle occupants or other road users. These issues can range from malfunctions in braking systems to defects in airbag deployment mechanisms, potentially leading to accidents or injuries. The goal is to minimize the risk of harm by promptly addressing the identified problem. Manufacturers conduct rigorous testing and evaluations to determine whether a defect warrants a recall, considering factors like potential impact on safety, frequency of occurrence, and severity of the potential consequences.
Types of Vehicle Recalls
Vehicle recalls are often categorized based on severity and impact. These classifications can assist owners in understanding the potential consequences of a recall.
- Minor Recalls: These typically involve issues that do not directly impact the vehicle’s safety, such as minor interior trim or electronic system malfunctions that do not pose an immediate threat. The impact on the consumer is often limited to a potential inconvenience, such as a minor repair or adjustment.
- Major Recalls: These recalls address issues that could lead to serious safety risks, potentially causing accidents or injuries. Examples include defects in braking systems, steering mechanisms, or potentially even tire failure. The impact on the consumer is substantial and potentially severe, requiring prompt attention to avoid potential accidents.
- Safety-Critical Recalls: These represent the most serious recalls and address defects that have the highest potential for catastrophic consequences. These recalls often involve issues that could lead to vehicle fires, loss of control, or other life-threatening situations. Immediate attention is vital in these instances to mitigate potential harm.
Legal and Regulatory Frameworks
Various jurisdictions have established legal and regulatory frameworks to govern vehicle recalls. These frameworks aim to ensure that manufacturers are accountable for safety issues in their products. These regulations often dictate the procedures for identifying, reporting, and addressing defects, as well as the communication methods required to inform affected vehicle owners.
Vehicle recalls can sometimes be a hassle, but they’re crucial for safety. One component often included in these recalls is wiper blades, like the ones discussed at wiper blades. These replacements ensure clear visibility, which is vital for safe driving. Ultimately, recalls are all about maintaining optimal vehicle function and driver safety.
Historical Context of Vehicle Recalls
A review of historical vehicle recalls reveals a pattern of safety issues and the associated responses. The consequences of these incidents can vary significantly, ranging from minor inconvenience to catastrophic accidents and significant financial losses. Understanding these past events provides valuable insights into the evolution of recall procedures and the ongoing commitment to public safety in the automotive industry.
For example, the numerous recalls related to certain types of airbags, or the significant issues with fuel tanks in certain models, underscore the importance of robust safety measures and procedures in the manufacturing process.
Recall Communication Strategies
Effective communication is critical during vehicle recalls. Clear, concise, and timely information ensures owner safety and helps maintain public trust. A well-designed communication strategy minimizes confusion and fosters a positive response to the recall process. This involves utilizing various channels to reach a broad audience while addressing concerns promptly and effectively.
Effective Methods for Communicating Recall Information
Vehicle owners must receive clear and timely recall notices. Communication methods should be tailored to reach a broad spectrum of owners, considering factors like language preferences, access to technology, and cultural nuances. This approach ensures everyone receives the vital information needed to address the issue. Utilizing multiple channels—such as mail, email, SMS, and online portals—increases the likelihood that owners will receive the critical notification.
Multi-Channel Recall Notification System
A comprehensive recall notification system employs multiple channels to reach owners efficiently. This framework should incorporate a central database for recall information, enabling automated communication based on vehicle identification numbers (VINs). This streamlined approach ensures timely notifications, regardless of owner location or communication preferences.
- Mail: Traditional mail remains a reliable method, particularly for owners who may not have consistent internet access or prefer physical notices. Printed materials should be clear, concise, and visually appealing to grab attention.
- Email: Email is an effective way to deliver personalized recall notices, providing tailored instructions and links to online resources. The email should be easily accessible and provide clear next steps for the owner.
- SMS: Short Message Service (SMS) can be employed to send concise recall notifications to owners who primarily use mobile phones. This provides an immediate alert, encouraging prompt action.
- Online Portals: Dedicated online portals or manufacturer websites provide comprehensive recall information, frequently asked questions (FAQs), and personalized owner dashboards. This offers a convenient resource for owners to understand the recall and their specific vehicle.
Importance of Clear and Concise Language
Clear and concise language is paramount in recall notices. Jargon and technical terms should be avoided, ensuring the information is easily understood by all vehicle owners. Precise language prevents misinterpretations and facilitates prompt action. This includes using simple sentence structures and avoiding overly complex terminology.
Addressing Customer Concerns and Anxieties
Addressing customer concerns and anxieties during recalls is crucial for maintaining trust. Providing multiple avenues for contact, such as dedicated phone lines or online chat, allows owners to ask questions and express concerns. Responding promptly and professionally to inquiries fosters a sense of security and trust in the manufacturer. This proactive approach addresses concerns directly, thereby mitigating anxieties and ensuring a smooth recall process.
Creating an FAQ Section Regarding Vehicle Recalls
A well-structured FAQ section is a valuable resource for vehicle owners. This section should address common questions related to the recall, such as eligibility, repair procedures, and potential costs. Providing clear answers to frequently asked questions minimizes confusion and empowers owners with the information they need. The FAQs should be easily accessible and updated promptly to reflect any changes or new information regarding the recall.
Recall Impact Analysis
Vehicle recalls, while necessary for safety, often have significant financial and operational implications for both manufacturers and consumers. Understanding these impacts is crucial for effective recall management and mitigation strategies. The costs associated with recalls can range from straightforward repair expenses to more complex disruptions in production and market perception.
Financial Implications for Manufacturers
Manufacturers face substantial financial burdens during a recall. These costs encompass not only the direct expenses of repairing or replacing defective parts but also the indirect costs associated with administrative procedures, public relations efforts, and potential legal liabilities. For instance, a large-scale recall can quickly escalate repair costs, potentially impacting a manufacturer’s bottom line. The Toyota unintended acceleration recalls of the early 2010s illustrate the substantial financial burden of a major recall, impacting the company’s profits and market share.
Financial Implications for Consumers
Consumers, too, experience financial repercussions from vehicle recalls. The costs can range from the inconvenience of scheduling repairs to the potential cost of repairs themselves. In some cases, consumers may be entitled to reimbursement for expenses related to the recall, though the process can be complex.
Recall Impact on Vehicle Types
The costs associated with a recall can vary significantly depending on the type of vehicle. Complex vehicles, such as luxury cars or heavy-duty trucks, often have more intricate systems and parts, leading to higher repair costs compared to simpler models. The costs of parts and labor also fluctuate based on the specific vehicle model.
Impact on Vehicle Sales and Market Reputation
A recall can negatively impact a manufacturer’s vehicle sales and market reputation. Consumer confidence can be shaken, potentially leading to decreased sales of affected models. A prolonged or poorly managed recall can severely damage the brand’s reputation and public image. The 2015 Volkswagen emissions scandal is a stark example of how a recall can negatively affect a manufacturer’s image and long-term sales prospects.
Supply Chain and Production Schedule Disruptions
Vehicle recalls can disrupt supply chains and production schedules. Manufacturers need to coordinate the recall process with parts suppliers and dealerships, which can lead to delays in production and logistical challenges. This disruption can ripple through the supply chain, impacting various industries involved in the production and distribution of vehicles. The impact is greater when the recalled part is critical to production or the supply chain is complex.
Risk Prediction and Mitigation Framework
A proactive approach to predicting and mitigating recall risks is crucial. Manufacturers should implement robust quality control measures throughout the production process to reduce the likelihood of defects. Thorough testing and validation procedures can help identify potential issues early on. A structured risk assessment framework can help manufacturers analyze potential recall scenarios and estimate potential costs. A well-defined communication strategy, involving all stakeholders, can also help mitigate negative impacts on the brand’s reputation.
By combining rigorous quality control, risk assessment, and a clear communication plan, manufacturers can minimize the negative consequences of vehicle recalls.
Recall Management Processes
Effective vehicle recall management is crucial for maintaining consumer safety and upholding brand reputation. A well-defined process ensures prompt and thorough handling of defects, minimizing potential harm and maximizing the efficiency of the recall campaign. A robust system for investigating, evaluating, and communicating about recalls is essential.
Initiating a Vehicle Recall Investigation
A systematic investigation process is vital for accurately identifying the root cause of a vehicle defect. This typically begins with receiving reports from various sources, including customer complaints, internal quality checks, and regulatory agency communications. A dedicated team, comprising engineers, quality control personnel, and legal experts, investigates the reports to assess the potential impact and severity of the defect.
Thorough analysis of data, including field reports, production records, and component specifications, is crucial to determine the extent of the problem.
Evaluating Severity and Scope of a Vehicle Defect
Evaluating the severity and scope of a vehicle defect is a critical step in managing a recall. This involves assessing the potential harm to consumers, analyzing the number of affected vehicles, and determining the geographical distribution of affected units. This evaluation should also consider the potential for secondary failures or issues resulting from the defect. A quantitative assessment of the potential harm, such as the likelihood of accidents, injuries, or property damage, is a critical component.
The extent of the defect’s scope should also consider the production period, affected model years, and specific vehicle configurations involved.
Role of Stakeholders in the Recall Process
Various stakeholders play distinct roles in the recall process. Manufacturers are responsible for initiating and managing the recall campaign, ensuring compliance with regulatory requirements, and communicating effectively with affected parties. Regulatory agencies, such as the National Highway Traffic Safety Administration (NHTSA) in the US, oversee the recall process, ensuring compliance with safety standards and consumer protection laws. Dealers play a vital role in notifying customers about the recall and performing the necessary repairs.
Customers are an integral part of the process by responding to recall notices and cooperating with repair procedures. A clear understanding of each stakeholder’s responsibilities and expectations is critical for a smooth and efficient recall.
Informing Regulatory Bodies and Affected Parties
Prompt and transparent communication with regulatory bodies and affected parties is essential for a successful recall. Manufacturers must promptly notify regulatory agencies of the identified defect and the proposed recall action. This notification must include a comprehensive description of the defect, the affected vehicle models and production periods, and the proposed corrective actions. Likewise, affected customers must be informed via clear and concise communication channels, such as mail, email, and online portals.
This communication should include details about the defect, repair procedures, and contact information for assistance.
Tracking Recall Campaign Progress
Efficiently tracking the progress of a recall campaign is essential for ensuring its effectiveness and minimizing its impact. A robust system for monitoring the number of vehicles repaired, the identification of any emerging issues, and the overall completion rate is required. Regular reporting on the recall progress to regulatory agencies and stakeholders is crucial. Real-time data dashboards can be employed to provide an overview of the recall campaign’s progress.
This system should allow for identification of potential bottlenecks and deviations from the planned schedule, enabling proactive adjustments and preventing delays.
Safety and Quality Considerations
Vehicle recalls are a critical aspect of maintaining public safety and upholding manufacturer responsibility. Proactive measures in safety and quality are paramount to preventing recalls and mitigating potential risks. This section explores the crucial role of safety considerations in preventing recalls, detailing quality control measures and the importance of testing, validation, and consumer feedback in ensuring vehicle safety.
Importance of Vehicle Safety in Preventing Recalls
Vehicle safety is paramount in preventing recalls. A robust design process, incorporating rigorous testing and validation procedures, significantly reduces the likelihood of defects that could lead to recalls. A focus on safety from the outset helps to avoid issues that could compromise the safety of vehicle occupants and other road users. Prioritizing safety in the design phase reduces the potential for costly and time-consuming recalls down the line.
Quality Control Measures by Manufacturers
Manufacturers employ various quality control measures to minimize defects and ensure the safety of their vehicles. These measures often include rigorous inspections at different stages of production, from component manufacturing to final assembly. Advanced testing equipment and trained personnel play a critical role in identifying potential defects early in the process. Regular audits and performance evaluations help to ensure ongoing adherence to quality standards.
For example, many manufacturers use statistical process control (SPC) methods to monitor production processes and identify any deviations from expected quality levels.
Role of Testing and Validation Procedures, Vehicle recall
Testing and validation procedures are fundamental to the design and production of vehicles. Rigorous testing in controlled environments helps identify potential weaknesses and areas for improvement. This includes crash testing, performance evaluations, and simulations to assess the vehicle’s response to various conditions. The results of these tests are analyzed to identify and address any safety concerns. Data from these procedures is vital for continuous improvement and refinement of design parameters.
A failure mode and effects analysis (FMEA) is a systematic approach used to identify potential failures and their impact.
Role of Consumer Feedback in Identifying Potential Safety Hazards
Consumer feedback plays a crucial role in identifying potential safety hazards. Manufacturers actively collect and analyze consumer reports, complaints, and feedback from various sources. This information can highlight issues that may not have been identified through internal testing or validation. For instance, online forums, social media platforms, and customer service interactions can provide valuable insights into potential safety concerns.
By monitoring these feedback channels, manufacturers can identify patterns and address potential problems proactively. Consumer feedback mechanisms are often integrated into product development cycles to inform design decisions.
Importance of Post-Recall Monitoring
Post-recall monitoring is crucial to preventing recurrence of the same safety issue. Manufacturers monitor the effectiveness of the recall remedies and analyze any reported issues arising after the recall is implemented. This analysis allows them to refine their quality control processes and identify areas where further improvements are needed. Tracking reported problems, both during and after the recall, can provide insights into the effectiveness of the corrective action and identify potential systemic issues.
Analysis of reported problems helps to prevent future recalls and ensure ongoing vehicle safety.
Data Analysis in Recalls
Data analysis plays a crucial role in effective vehicle recall management. By identifying patterns and trends in reported defects, manufacturers can proactively address potential safety issues, minimize negative impact on customers, and enhance the overall quality of their vehicles. A robust data analysis approach is vital for predicting future recall needs, optimizing recall processes, and ensuring the safety of millions of vehicles on the road.A comprehensive data analysis strategy in vehicle recalls involves several key aspects, including the identification of trends and patterns in vehicle defects, the assessment of risk associated with specific components or systems, the prediction of potential future recall issues, and the establishment of a structured data organization system.
Ethical considerations are paramount in the use of this data.
Identifying Trends and Patterns in Vehicle Defects
Analyzing defect reports, service records, and warranty claims provides insights into common issues. For example, if multiple vehicles of the same model year exhibit a specific electrical malfunction under certain conditions, this suggests a potential design flaw. Statistical methods, such as frequency analysis and trend analysis, can help identify recurring problems and pinpoint potential areas of concern.
Assessing Risk Associated with Components or Systems
Statistical methods such as failure rate analysis and reliability analysis help quantify the risk associated with specific components or systems. For instance, a high failure rate for a particular part in a given vehicle model suggests a potential safety concern, warranting further investigation and potential recall.
Predicting Future Potential Recall Issues
By analyzing historical data, manufacturers can predict potential future recall issues. If a certain component consistently demonstrates a high failure rate within a specific timeframe, it suggests a potential for future problems. This predictive analysis allows for proactive measures, such as redesigning components or implementing preventive maintenance procedures.
Example: Predicting Recall Issues
Consider a scenario where a particular type of braking system component exhibits a high failure rate within the first two years of use in a specific vehicle model. Analyzing data from warranty claims, service records, and customer complaints can help predict the potential need for a future recall. Proactive measures, such as issuing a service bulletin or redesigning the component, can mitigate the risk and improve safety.
Organizing Data Related to Recalls
A well-structured database is essential for managing recall data effectively. This database should include detailed information on the affected vehicle models, components, and defects, along with relevant repair procedures and customer contact information. Using standardized data fields and formats ensures data consistency and accuracy. This organized structure facilitates efficient retrieval and analysis of recall-related information.
Example: Database Structure
Vehicle Model | Component | Defect Description | Number of Affected Vehicles | Recall Date |
---|---|---|---|---|
2023 Sedan | Steering Column | Wobbly steering wheel | 10,000 | 2024-03-15 |
2023 SUV | Brake Pedal | Stuck pedal | 5,000 | 2024-04-01 |
Ethical Implications of Data Usage in Vehicle Recalls
The use of data in vehicle recalls raises ethical concerns. Transparency and accountability are paramount. Manufacturers must ensure that data is collected and used ethically, respecting individual privacy and confidentiality. The potential for bias in data analysis must be addressed, and mechanisms for data validation and verification should be in place. The importance of maintaining data security is also paramount.
International Variations
Vehicle recalls are a global issue, requiring harmonized but adaptable procedures across different jurisdictions. Differences in legal frameworks, cultural norms, and regulatory structures significantly impact how recalls are handled in various countries. Understanding these nuances is crucial for effective communication and successful recall management.
Comparison of Vehicle Recall Procedures
Different countries have distinct legal frameworks governing vehicle recalls. Some regions prioritize consumer safety above all else, while others may focus on balancing consumer rights with the manufacturer’s responsibilities. These variations lead to distinct procedures for initiating, implementing, and monitoring recalls. For example, the United States relies heavily on the National Highway Traffic Safety Administration (NHTSA) for recall coordination, whereas the European Union utilizes a more collaborative approach involving member state authorities.
Cultural Considerations in Recall Communication
Cultural differences play a critical role in recall communication strategies. Direct communication styles might be effective in some cultures, while indirect approaches are preferred in others. Understanding the cultural nuances of the target audience is essential for crafting a recall message that is both clear and respectful. Language barriers can also present significant challenges; accurate and culturally sensitive translations are vital for ensuring all affected consumers understand the recall information.
International Legal Frameworks
Various international legal frameworks and agreements influence vehicle recall procedures. These frameworks often establish common standards and guidelines, though the level of enforcement and implementation varies. For instance, the UNECE Regulations for the approval of vehicles can influence recall processes for specific vehicle components or systems. International standards and guidelines provide a baseline for national recall policies, though their application and interpretation can vary significantly across countries.
Roles of Regulatory Bodies
Regulatory bodies play a critical role in overseeing and coordinating vehicle recalls. These bodies, which may be national or regional, are responsible for ensuring that recalls are conducted efficiently and effectively. The regulatory body in each country determines the scope and procedure of the recall process. Different countries will have various regulatory bodies for recalls, including but not limited to transportation agencies, consumer protection organizations, or industry associations.
Table of International Recall Procedures
Country | Regulatory Body | Recall Process | Cultural Considerations |
---|---|---|---|
United States | NHTSA | Manufacturer-driven, with NHTSA oversight. Strict deadlines and requirements. | Direct communication, emphasis on consumer rights. |
European Union | European Commission and national authorities | Collaborative approach, with member states having a role. | Emphasis on consumer safety, varying communication styles across member states. |
Japan | Ministry of Land, Infrastructure, Transport and Tourism | Emphasis on promptness and efficiency, often involving manufacturer cooperation. | Indirect communication, strong sense of community. |
China | State Administration for Market Regulation | Emphasis on consumer safety and swift action. | Cultural sensitivity in language and approach. |
Customer Support During Recalls: Vehicle Recall
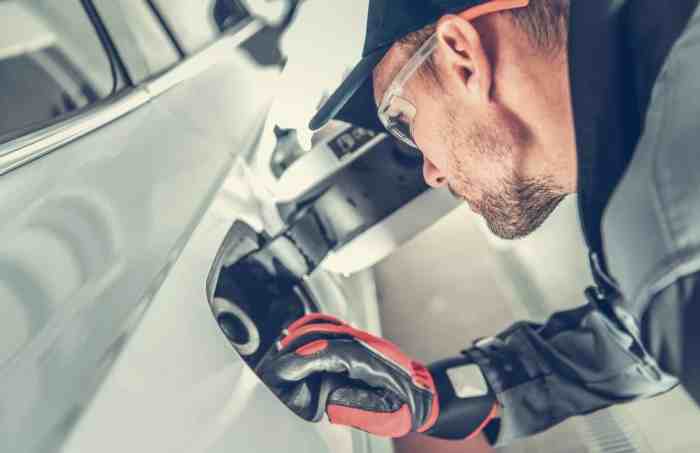
A robust customer support system is critical during vehicle recalls. It’s paramount to address customer concerns promptly and effectively, ensuring a smooth and transparent process. A well-structured system builds trust and fosters a positive customer experience, even amidst a potentially stressful situation.Effective customer support minimizes negative publicity and maintains brand reputation. It facilitates a proactive and informed approach to handling the recall, mitigating potential safety risks and financial burdens.
Establishing a Robust Customer Support System
A well-structured customer support system during recalls requires clear communication channels and trained personnel. This involves providing multiple avenues for customer inquiries, such as dedicated phone lines, email addresses, and online portals. These channels should be easily accessible and consistently monitored. Comprehensive training for customer service representatives is essential to equip them with the knowledge and skills to handle a high volume of inquiries efficiently and accurately.
Training should encompass recall procedures, relevant regulations, and best practices for resolving customer concerns.
Importance of Timely and Accurate Information
Providing timely and accurate information to customers is critical. Customers must receive clear and concise details about the recall, including the specific vehicles affected, the nature of the defect, and the recommended corrective action. This includes readily available and easily understandable documentation, such as recall notices, repair procedures, and contact information. Delays in disseminating information can erode customer trust and potentially lead to safety risks.
Role of Customer Service Representatives
Customer service representatives play a vital role in handling recall-related inquiries. They must be equipped to answer customer questions thoroughly and patiently, providing accurate and consistent information. They should be authorized to address customer concerns, including those regarding the repair process, costs, and potential inconvenience. Representatives should also be trained to identify and escalate complex or sensitive customer situations to management.
Resolving Customer Complaints Efficiently
A well-defined process for resolving customer complaints is crucial. Establishing a clear escalation path, providing multiple communication channels, and ensuring prompt responses are key. Implementing a system for tracking and resolving complaints ensures that issues are addressed systematically. This involves a process to document complaints, assign responsibility for resolution, and follow up with customers until satisfaction is achieved.
Building Trust with Customers During Recalls
Building trust with customers during recalls is paramount. Transparency, honesty, and prompt communication are vital. Providing accurate and timely information, actively addressing customer concerns, and ensuring a smooth repair process are key elements. Demonstrating empathy and understanding towards the customer’s situation fosters trust and confidence in the brand. A commitment to resolving issues swiftly and effectively, coupled with clear communication throughout the process, significantly strengthens customer relationships.
Long-Term Impacts of Recalls
Vehicle recalls, while crucial for safety, can have lasting repercussions on a manufacturer’s brand image and market position. Understanding these potential long-term effects is vital for proactive management and mitigating negative impacts. A well-executed recall strategy should consider not only the immediate safety concerns but also the long-term effects on brand reputation, consumer trust, and market share.The long-term impact of vehicle recalls extends beyond the immediate crisis.
Negative publicity can linger, impacting brand perception and potentially driving customers away. A comprehensive approach to recall management must account for these enduring effects to ensure the long-term health of the company.
Brand Reputation Damage
The fallout from a major recall can severely damage a manufacturer’s brand reputation. Consumer perception shifts, and trust is eroded. Negative media coverage, social media chatter, and customer dissatisfaction contribute to a tarnished image. The damage can be amplified by the scale of the recall, the severity of the defect, and the manufacturer’s response. For example, the 2014 Takata airbag recall, one of the largest in history, significantly impacted the reputation of several automakers.
Impact on Consumer Trust
Consumer trust is a critical asset for any vehicle manufacturer. A recall, particularly a major one, can erode this trust, potentially leading to a decline in sales and customer loyalty. Transparency and a swift, well-communicated response are essential to mitigate the damage. Consumers who experience a problem due to a recall are likely to seek alternatives from competitors, negatively impacting the manufacturer’s market share.
Companies that demonstrate a proactive and transparent approach to recalls tend to retain more customer trust.
Strategies for Rebuilding Consumer Trust
Rebuilding consumer trust after a major recall requires a multi-faceted approach. Open communication with customers, proactive engagement on social media, and demonstrable commitment to safety are crucial. A commitment to quality improvements and rigorous testing can help reassure customers. For example, a manufacturer might publicly announce enhanced safety protocols or investments in new technology. Providing ongoing support and addressing customer concerns directly are vital steps in restoring trust.
Identifying Lasting Effects on Market Share
A recall can impact market share, especially if the affected model is a significant portion of the manufacturer’s sales. A systematic analysis of sales data before, during, and after the recall is essential. Factors like competitor actions, economic conditions, and the overall market trend must be considered when evaluating the lasting effects on market share. The analysis should consider the specific market segments affected by the recall and assess the long-term impact on brand perception in these segments.
Comparative data on competitor sales figures during the same period can help gauge the magnitude of the impact.
Managing and Mitigating Negative Press
Negative press during a recall can be extensive. A proactive approach is essential to manage and mitigate the negative publicity. Transparency, honesty, and a clear communication strategy are key. The company should issue timely and accurate statements addressing the recall, its impact, and the measures being taken to rectify the issue. A dedicated communication team should be in place to respond to media inquiries and address customer concerns.
A well-prepared crisis communication plan can significantly reduce the long-term damage.
Recall Prevention Strategies
Proactive measures to prevent vehicle defects are crucial for maintaining consumer safety and reducing the frequency and impact of recalls. A robust preventative strategy encompasses various aspects of vehicle design, production, and quality control. By anticipating potential issues and implementing rigorous testing and feedback mechanisms, manufacturers can minimize the likelihood of defects emerging in the field.Effective recall prevention strategies go beyond simply identifying and fixing problems after they arise; they focus on building resilience into the entire vehicle development and production cycle.
This proactive approach saves considerable time, resources, and, most importantly, minimizes potential harm to consumers.
Design Strategies for Defect Prevention
Comprehensive design reviews, utilizing robust simulations and virtual testing, can identify potential vulnerabilities in the vehicle’s design. Employing advanced engineering analysis tools, such as finite element analysis (FEA), enables manufacturers to model and predict stress concentrations, material fatigue, and other factors that could lead to component failure. These simulations are often used to refine design parameters and optimize component configurations, minimizing potential weaknesses before production begins.
For example, improved materials selection or modified component geometries can mitigate risks.
Improving Design and Production Processes
Implementing standardized procedures and protocols for design and production is essential for minimizing inconsistencies and errors. This involves creating detailed manufacturing specifications, clear work instructions, and rigorous quality checks at each stage of the production process. Standardized processes enhance consistency and predictability, reducing the likelihood of defects arising from human error. Employing lean manufacturing principles can further streamline processes, reduce waste, and improve efficiency.
Vehicle recalls can be a pain, but they’re often crucial for safety. Properly functioning car lights, like those found at car lights , are essential for visibility and avoiding accidents. Ultimately, recalls are a vital part of keeping our roads safe for everyone.
For instance, establishing clear communication channels between design, engineering, and manufacturing teams, and establishing an environment of shared responsibility, can improve coordination and prevent errors.
Proactive Quality Control Measures
Implementing proactive quality control measures throughout the manufacturing process is vital for catching defects early. This includes regular inspections of components and assemblies, along with stringent testing procedures for each stage of the production line. Employing advanced quality control technologies, such as automated inspection systems, can significantly increase the speed and accuracy of defect detection. Furthermore, establishing a robust system for managing and tracking defects throughout the manufacturing process is crucial.
This allows for timely corrective actions and prevents recurrence. For instance, using statistical process control (SPC) charts can monitor and analyze production data to identify trends and potential issues early on.
Vehicle Testing Procedures
A comprehensive vehicle testing program is necessary to validate the performance and durability of vehicles under various conditions. This program should include rigorous testing of components, systems, and the entire vehicle, simulating real-world scenarios like extreme temperatures, varying road surfaces, and heavy loads. Testing should cover not only functional performance but also durability and reliability. Testing methods should be regularly updated and adapted to reflect advancements in vehicle technology and evolving safety standards.
For instance, crash tests should be performed using advanced dummies and simulation software to better replicate human injuries and provide more accurate data.
Customer Feedback Incorporation
Incorporating customer feedback into the design process is crucial for understanding and addressing potential issues from a user perspective. Customer feedback, gathered through surveys, online forums, and direct interaction, can offer valuable insights into areas where the vehicle design could be improved. This feedback can range from minor ergonomic issues to more substantial design flaws. For example, establishing customer feedback channels and creating dedicated teams to analyze and implement suggestions can create a more user-centric design approach.
Case Studies of Vehicle Recalls
Examining past vehicle recalls provides valuable insights into effective and ineffective recall management strategies. Understanding the factors that contribute to successful outcomes and the pitfalls of poorly executed recalls is crucial for preventing future incidents and enhancing public safety. By analyzing case studies, we can learn from both successes and failures, leading to more robust and customer-centric recall processes.A comprehensive analysis of past vehicle recalls reveals a wide spectrum of experiences, ranging from smooth and efficient processes to complex and costly interventions.
The success or failure of a recall often hinges on several intertwined factors, including the promptness of action, the clarity of communication, and the thoroughness of the corrective actions. This section delves into specific case studies to illustrate these points.
Successful Recall Management Strategies
Effective recall management often involves a multi-faceted approach, combining swift action with transparent communication. A crucial component is rapid identification of the problem, allowing for a prompt response. This includes immediate notification of the affected vehicle owners, ensuring clear and concise information about the potential risks and necessary actions. This proactive communication builds trust and helps mitigate customer concerns.
Furthermore, the recall process should be efficient and well-organized, minimizing delays and maximizing the number of vehicles repaired.
- Example 1: A manufacturer’s prompt response to a potential brake-system defect, resulting in a swift recall and a clear communication plan, successfully prevented significant injuries. The manufacturer swiftly issued a detailed notification explaining the issue, the potential consequences, and the repair procedure. This proactive approach effectively reassured customers, fostering trust and minimizing any potential panic.
- Example 2: A recall involving a faulty airbag inflator was handled with meticulous attention to detail. The manufacturer, through rigorous testing and collaboration with safety authorities, quickly pinpointed the exact cause of the issue and implemented a comprehensive repair strategy. This precision led to minimal disruption to customer service and a high rate of vehicle repairs.
Poorly Handled Recalls and Their Consequences
Ineffective recall management can have significant repercussions, ranging from damaged brand reputation to substantial financial losses. A critical aspect is the timely and accurate identification of the defect. Delayed action can expose more vehicles to risk and lead to a wider scope of the recall. A lack of transparency in communication can erode public trust and damage the manufacturer’s reputation.
- Example 1: A delayed recall of a vehicle model due to a critical engine defect resulted in several accidents and injuries. The manufacturer’s initial response was slow and lacked clarity, leading to public distrust and a significant drop in sales. The company faced substantial legal repercussions and reputational damage.
- Example 2: A recall involving a faulty steering system was met with confusion and concern due to the ambiguity in the communication. The manufacturer’s explanation of the problem and the repair procedure was unclear, causing significant customer anxiety. This lack of clarity negatively impacted customer confidence and brand image.
Factors Contributing to Successful and Unsuccessful Recall Outcomes
Several factors contribute to the success or failure of a vehicle recall. A critical factor is the prompt and thorough investigation of the reported issue. A clear understanding of the defect’s nature and its potential impact on vehicle safety is essential. Effective communication is vital for maintaining public trust and ensuring a smooth recall process.
Factor | Successful Outcome | Unsuccessful Outcome |
---|---|---|
Investigation Thoroughness | Complete analysis of the defect and its implications. | Incomplete analysis, leading to inaccurate assessment of the problem. |
Communication Clarity | Clear and concise information to the public and affected owners. | Ambiguous or confusing information, leading to customer anxiety and distrust. |
Repair Efficiency | Efficient repair procedures and readily available parts. | Inefficient repair procedures and parts shortages. |
Lessons Learned from Past Recall Events
Analyzing past recalls reveals crucial lessons for improving future recall processes. A critical lesson is the importance of proactive measures to prevent future recalls. Furthermore, proactive risk assessments and preventative maintenance programs can help identify potential problems early.
“Proactive safety measures are paramount in preventing future recalls.”
Importance of Proactive Measures in Preventing Future Recalls
Proactive measures, such as rigorous quality control during manufacturing and ongoing safety assessments, can significantly reduce the likelihood of future recalls. This proactive approach involves continuous monitoring of vehicle performance and safety features, coupled with feedback mechanisms to address any potential issues. Furthermore, a culture of safety and quality within the organization can be instrumental in preventing future problems.
Closing Summary
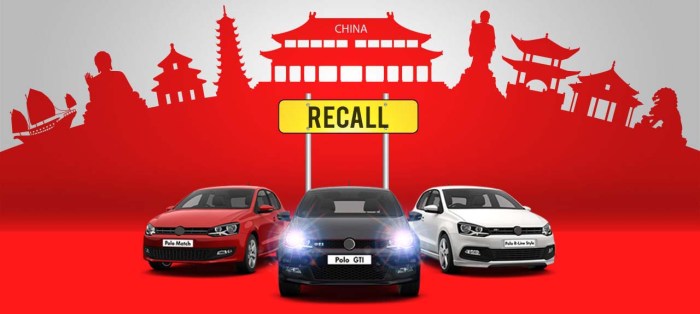
In conclusion, vehicle recalls are complex events impacting various stakeholders. Effective management requires a multi-faceted approach encompassing communication, financial analysis, safety considerations, and robust data analysis. Understanding the international variations, customer support needs, and long-term impacts is crucial for mitigating potential risks and building trust with consumers. Proactive recall prevention strategies, drawing upon lessons from case studies, are vital for maintaining public confidence and brand reputation.
Top FAQs
What are the common causes of vehicle recalls?
Vehicle recalls are often triggered by safety-related defects in components or systems, ranging from faulty brakes to potentially hazardous electrical wiring. Manufacturing errors, design flaws, or unforeseen issues in the field can all lead to recalls.
How long does a typical vehicle recall process take?
The duration of a vehicle recall varies significantly, depending on factors such as the defect’s severity, the number of affected vehicles, and the complexity of the repair procedures. It can range from a few weeks to several months.
What are the responsibilities of vehicle manufacturers during a recall?
Manufacturers have a legal obligation to promptly notify affected owners, provide clear repair instructions, and ensure that necessary parts are available. They are also responsible for managing the recall process effectively to minimize disruption and potential harm.
What are my rights as a vehicle owner during a recall?
Vehicle owners have the right to be promptly informed about any recall affecting their vehicle. They also have the right to receive clear and accurate information regarding the defect and the necessary repairs.